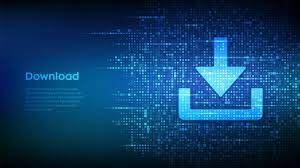
Keleş Ö, Blevins C, Bowman K (2017) Effect of build orientation on the mechanical reliability of 3D printed ABS. Wang C, Lin T, Hu S (2007) Optimizing the rapid prototyping process by integrating the Taguchi method with the Gray relational analysis. Compos B 99:506–513Īhn S, Montero M, Odell D, Roundy S et al (2002) Anisotropic material properties of fused deposition modeling ABS. Zou R, Xia Y, Liu S, Hu P et al (2016) Isotropic and anisotropic elasticity and yielding of 3D printed material. Palermo E (2013) Fused Deposition Modeling: Most Common 3D Printing Method. The research presented in this paper is the first of its kind to demonstrate an effective low cost, continuous variable density infill for FDM applications an improvement on the discrete infill assignment that is currently available in commercial slicers. Mass neutral optimized designs yielded 37–39% failure strength improvement compared to the best commercial counterparts while maintaining or slightly improving print time. Utilization of the infill design methodology in an automotive and aerospace component was successfully demonstrated highlighting the immediate applicability of the technique. The location of failure migrated from regions containing stress risers to the designed failure point as local reinforcement was increased. The uniaxial tensile tests demonstrated a distinct improvement from the baseline commercial product to the optimized configurations produced from the methodology presented. The purpose of this paper is to present a methodology and experimental results for the design of continuous 2D infill in FDM parts, improving on the common commercial patterns widely used. Traditionally, a homogenous infill pattern is utilized over the entire domain of the structure, which over supports lightly loaded areas, while highly stressed regions are under supported. With a recent expansion into structural applications and prevalent focus on mass reduction to meet fuel efficiency targets, semi-dense components can be used to provide the necessary structural support while simultaneously reducing mass and print time. The popularity of 3D printed parts continues to grow, seeing increased use in the design, medical, and engineering fields.
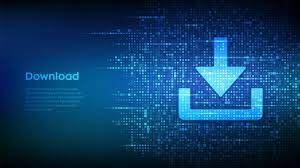